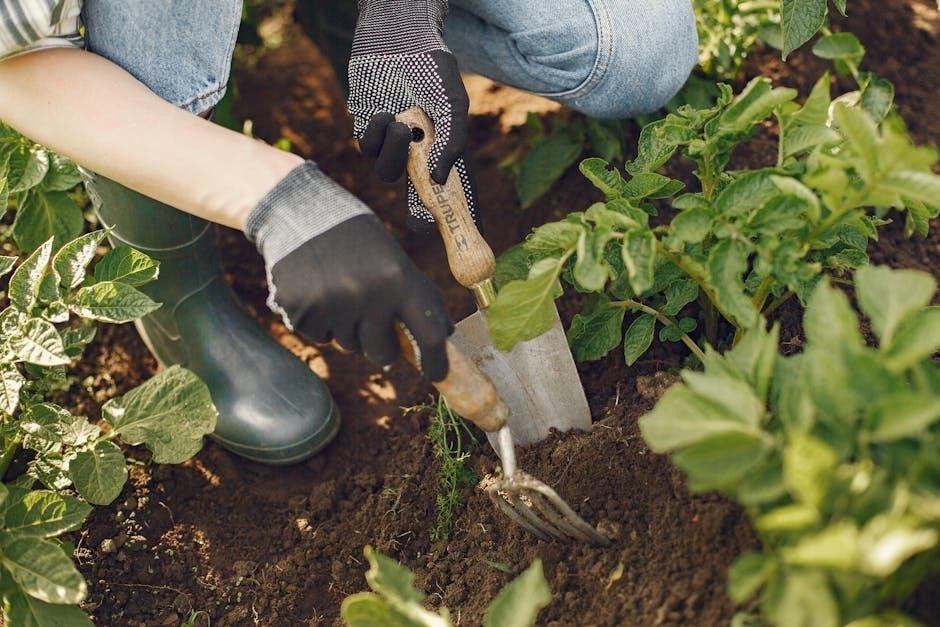
Manual fork lifts are essential tools for lifting and moving materials in various industries. They are manually operated, ensuring efficiency and safety in material handling tasks.
1.1 Definition and Purpose
A manual fork lift, also known as a hand-operated fork lift, is a portable device designed to lift, move, and position materials. It operates without electric or hydraulic power, relying on manual effort to elevate loads. Its primary purpose is to assist in material handling tasks, providing a cost-effective and efficient solution for small to medium-sized operations. Unlike motorized versions, manual fork lifts are lightweight and easy to maneuver, making them ideal for tight spaces and lighter loads.
1.2 Brief History and Evolution
The manual fork lift traces its origins to the early 20th century, evolving from basic lifting tools to more refined designs. Initially used in industrial settings, these devices were simple, relying on manual effort to lift and move materials. Over time, improvements in design, materials, and ergonomics have enhanced their functionality and safety. Despite advancements in powered alternatives, manual fork lifts remain essential for their portability and cost-effectiveness in smaller operations.
1.3 Importance in Material Handling
Manual fork lifts play a crucial role in material handling by enabling efficient and safe movement of goods. Their compact design and maneuverability make them ideal for tight spaces, optimizing workflow in warehouses and distribution centers. By reducing reliance on larger machinery, they lower operational costs while maintaining productivity. This versatility ensures they remain indispensable in various industries, enhancing overall material handling efficiency and contributing to smoother operational processes across sectors.
Key Components of a Manual Fork Lift
Manual fork lifts consist of a hydraulic system for lifting, sturdy forks for load handling, durable wheels for smooth maneuverability, and an ergonomic handle for easy control.
2.1 Hydraulic System
The hydraulic system in a manual fork lift is essential for lifting and lowering loads. It operates using a hand pump to pressurize fluid, which then powers a cylinder to lift the forks. This system requires minimal maintenance but must be checked regularly for leaks or damage to ensure smooth operation. Proper hydraulic function ensures safety and efficiency in material handling tasks. Regular inspections are crucial to prevent failures and maintain optimal performance.
2;2 Forks and Load-Carrying Mechanism
The forks are the primary components responsible for lifting and securing loads. Typically made of steel, they vary in thickness and width to accommodate different load sizes. Securely attached to the lift, they are designed to withstand heavy weights while maintaining stability. The load-carrying mechanism ensures smooth operation, allowing the forks to tilt and elevate loads safely. Proper alignment and maintenance of the forks are crucial for optimal performance and safety in material handling tasks. Regular inspections prevent potential failures.
2.3 Wheels and Maneuverability
The wheels of a manual fork lift are designed for smooth maneuverability across various surfaces. Made from durable materials like nylon or rubber, they provide traction and stability. The wheels’ size and tread pattern ensure easy navigation in tight spaces, while their construction allows for minimal effort when pushing or pulling heavy loads. Proper wheel maintenance, including lubrication and cleanliness, is essential for optimal performance and longevity. This design enhances operational efficiency in industrial environments.
2.4 Handle and Control Mechanisms
The handle and control mechanisms of a manual fork lift are crucial for precise operation. Ergonomically designed handles reduce user fatigue, while intuitive controls allow for easy lifting and lowering. These mechanisms typically include a pump handle for hydraulic lifting and directional controls for maneuvering. Proper grip and leverage ensure safe and efficient load management, minimizing strain on the operator and enhancing overall productivity in material handling tasks. Regular maintenance of these components is essential for smooth operation.
Operational Safety Guidelines
Operational safety guidelines for manual fork lifts emphasize pre-operation checks, proper lifting techniques, load stability, and emergency procedures to ensure safe and efficient material handling. Regular training is essential.
3.1 Pre-Operation Safety Checks
Pre-operation safety checks for manual fork lifts are crucial to ensure safe and efficient use. Operators should inspect the hydraulic system for leaks, check the condition of wheels and tires, and verify the stability of the forks. Additionally, they must ensure all control mechanisms are functioning properly and that the load-carrying capacity is not exceeded. Regular lubrication of moving parts and inspection of safety accessories, like brakes, are also essential to prevent accidents and maintain optimal performance.
3.2 Proper Lifting Techniques
Proper lifting techniques are vital for safe and efficient operation of manual fork lifts. Operators should approach the load squarely, ensure the forks are aligned with the center of the load, and lift smoothly without jerking. The load should be kept low and balanced, with clear visibility maintained. Operators must avoid overreaching or leaning, as this could compromise stability. Proper lifting techniques minimize the risk of accidents and ensure the longevity of the equipment.
3.3 Load Stability and Balance
Load stability and balance are critical for safe manual fork lift operation. Ensuring the load is centered on the forks prevents tipping. Operators should secure unstable loads and avoid overloading. Moving at a steady pace and avoiding sudden turns maintains balance. Proper load arrangement and even weight distribution are essential. Operators must always ensure clear visibility and maintain control. Improper balance can lead to accidents, making adherence to these practices paramount for workplace safety and operational efficiency.
3.4 Emergency Procedures
In case of emergencies, operators must follow specific procedures to ensure safety. First, assess the situation and secure the load if possible. Move the fork lift to a safe area and engage the brake. If damage occurs, stop operation and inspect the unit. Notify supervisors immediately. Operators should be trained in emergency protocols, including proper evacuation and incident reporting. Regular drills and clear communication channels are essential for effective emergency response. Always document incidents for future reference.
Maintenance and Repair
Regular maintenance ensures optimal performance and longevity of manual fork lifts. Inspect hydraulic systems, lubricate moving parts, and address wear and tear promptly. Follow manufacturer guidelines for repairs.
4.1 Regular Maintenance Schedule
A regular maintenance schedule is crucial for manual fork lifts to ensure safety and efficiency. Daily checks should include inspecting hydraulic fluid levels, tire condition, and fork alignment. Weekly, lubricate moving parts and clean the handlebars. Monthly, inspect the hydraulic system for leaks and test the load-lifting mechanism. Always follow the manufacturer’s guidelines for maintenance intervals and record all inspections to track equipment health and prevent unforeseen breakdowns. Regular upkeep extends the lifespan of the fork lift and ensures reliable performance.
4.2 Common Wear and Tear Issues
Manual fork lifts often experience wear and tear in the hydraulic system, leading to fluid leakage and seal degradation. The forks can bend or corrode over time, affecting load-carrying capacity. Wheels may wear down or sustain damage from rough surfaces, impacting maneuverability. Additionally, the handle and control mechanisms can show signs of wear due to frequent use. Regular maintenance is essential to address these issues and prevent equipment failure.
4.3 Troubleshooting Techniques
To address issues with manual fork lifts, start by identifying common problems such as hydraulic system leaks or bent forks. Inspect the lift regularly for signs of wear. Check for fluid leaks by examining hydraulic lines and seals. Look for misalignment or damage in the load-carrying mechanism. Test the wheels on different surfaces to ensure smooth operation. Addressing these issues promptly through maintenance and repair can prevent further damage and ensure safe operation.
Applications Across Industries
Manual fork lifts are widely used in warehousing, manufacturing, and retail for moving goods. They are versatile tools for handling materials in construction and outdoor settings efficiently.
5.1 Warehousing and Distribution
Manual fork lifts are widely used in warehouses and distribution centers for efficient material handling. They enable easy loading, unloading, and organizing of goods, ensuring smooth operations. Their maneuverability and compact design make them ideal for navigating tight spaces, enhancing productivity. These tools are essential for maintaining order and efficiency in fast-paced environments, supporting timely delivery and inventory management. Their versatility ensures they remain a cornerstone in modern logistics and supply chain operations.
5.2 Manufacturing Plants
Manual fork lifts play a crucial role in manufacturing plants by efficiently moving raw materials, components, and finished goods. They ensure smooth production flows, reducing downtime and enhancing safety. Their compact design allows easy navigation through tight production areas, making them ideal for assembly lines and inventory management. By supporting precise material placement, manual fork lifts contribute to maintaining production schedules and overall operational efficiency in manufacturing environments.
5.3 Retail and Logistics
Manual fork lifts are indispensable in retail and logistics for efficiently managing inventory and streamlining operations. They enable quick restocking of shelves, movement of pallets, and organization of goods in warehouses. Their portability and ease of use make them ideal for navigating crowded retail spaces and ensuring timely delivery of products. By enhancing productivity and safety, manual fork lifts are vital for maintaining smooth workflows in both retail environments and logistics facilities.
5.4 Construction and Outdoor Use
Manual fork lifts are widely used in construction and outdoor settings for their durability and versatility. They efficiently handle heavy materials like bricks, steel, and equipment on uneven terrain. Their compact design allows easy maneuverability in tight spaces, making them ideal for construction sites and outdoor yards. Additionally, they are eco-friendly, producing no emissions, which is advantageous for outdoor projects. Their reliability in temporary or remote locations underscores their value in construction and outdoor logistics.
Manual fork lifts remain essential tools in material handling, offering efficiency and reliability across industries. Their simplicity and effectiveness ensure continued relevance in modern operations and future advancements.
6.1 Summary of Key Points
Manual fork lifts are versatile tools designed for efficient material handling, offering reliability across industries. Their simplicity enhances productivity while ensuring safety. Regular maintenance and proper operation are crucial for longevity and performance. Industries like warehousing and manufacturing benefit from their versatility. By following safety guidelines and maintaining equipment, businesses can maximize their utility and ensure smooth operations. Their enduring relevance underscores their importance in modern material management systems.
6.2 Future Trends in Manual Fork Lift Technology
Future trends in manual fork lift technology include advancements in ergonomic design, integration of smart technologies, and a focus on sustainability. Innovations like adjustable handles and lightweight materials aim to enhance operator comfort and efficiency. Additionally, the incorporation of AI-driven systems for performance monitoring and safety is expected. These developments will ensure manual fork lifts remain relevant in evolving industrial landscapes, supporting industries with improved productivity and environmental responsibility.