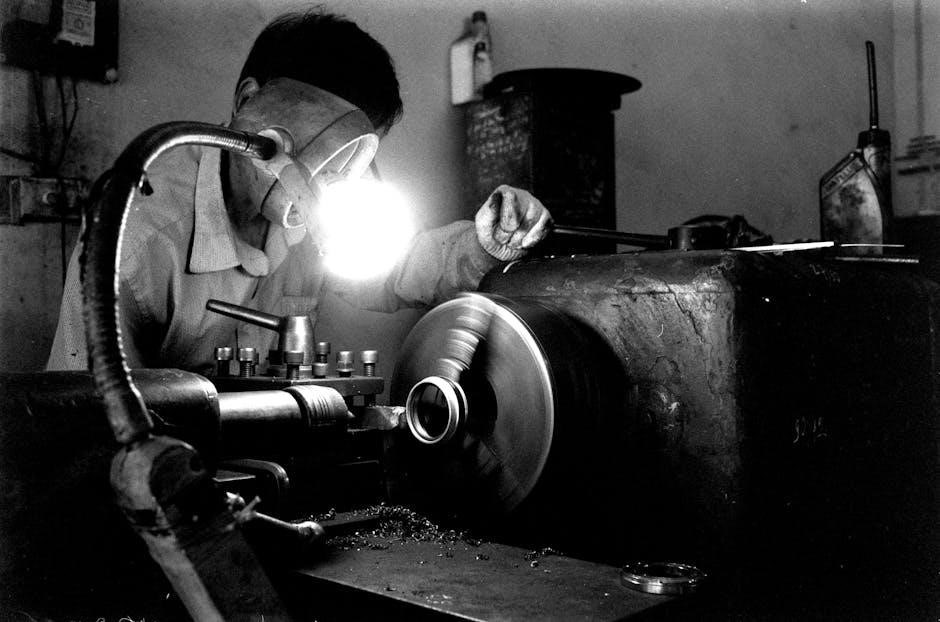
A manual machinist is a skilled tradesperson specializing in operating traditional, non-computerized machinery to craft precise metal components essential for manufacturing and engineering applications.
1.1 Definition and Role Overview
A manual machinist is a skilled tradesperson who operates and maintains traditional, non-computerized machine tools to fabricate precise metal components. Their role involves setting up machinery, interpreting blueprints, and performing manual machining, finishing, and assembly tasks. Proficiency in technical skills, attention to detail, and the ability to learn new techniques are essential for success in this position.
Key Responsibilities of a Manual Machinist
Manual machinists set up and operate manual machine tools, maintain equipment, and perform tasks requiring precision, such as cutting, grinding, and finishing metal components accurately.
2.1 Setting Up and Operating Manual Machine Tools
Manual machinists operate and set up equipment like lathes, milling machines, and grinders. They select appropriate tools, materials, and settings to ensure precise cuts and finishes. This involves calibrating machines, aligning workpieces, and making adjustments for optimal performance. Proficiency in operating these tools is crucial for producing accurate and high-quality components efficiently.
2.2 Maintaining and Repairing Machinery
Manual machinists are responsible for performing routine maintenance and repairs on machine tools to ensure optimal functionality. This includes lubricating moving parts, replacing worn components, and addressing mechanical issues promptly. They also conduct safety checks to prevent accidents and downtime, ensuring machinery operates efficiently and meets production standards. Regular upkeep is essential to maintain precision and extend equipment lifespan.
2.3 Reading and Interpreting Blueprints
Manual machinists must accurately interpret blueprints, sketches, and technical drawings to determine part dimensions, tolerances, and production sequences. This skill ensures precise fabrication, as they translate complex diagrams into actionable steps for machining. Understanding specifications is critical for producing components that meet exacting standards and fit seamlessly into larger assemblies or systems.
Skills and Qualifications Required
Manual machinists need strong technical skills, precision, and problem-solving abilities to operate machinery and produce accurate components, ensuring high-quality results consistently.
3.1 Technical Skills and Knowledge
Manual machinists must possess in-depth knowledge of machine tools, including lathes, milling machines, and grinders. Proficiency in interpreting blueprints, understanding metallurgy, and applying mathematical principles is essential. They should also be adept at using precision measuring instruments like micrometers and calipers to ensure dimensional accuracy. Strong technical skills enable them to troubleshoot and maintain equipment effectively, optimizing production processes.
3.2 Attention to Detail and Precision
Attention to detail is critical for manual machinists, as even minor errors can lead to inaccurate or defective parts. Precision is paramount in cutting, grinding, and finishing operations. Proficiency in using measuring tools like micrometers and calipers ensures dimensional accuracy. The ability to interpret blueprints and technical specifications further enhances their capacity to deliver high-quality, precise components consistently. Focus and concentration are essential in maintaining this level of accuracy.
Education and Training Pathways
Manual machinists typically start with a high school diploma, then pursue apprenticeships or vocational training. Certifications can enhance career prospects and demonstrate specialized expertise.
4.1 High School Diploma or Equivalent
A high school diploma or equivalent is typically required to enter manual machining. This foundational education provides essential math, science, and problem-solving skills. It serves as a stepping stone for further vocational training or apprenticeships, which are crucial for mastering machining techniques and tools. Employers often require this basic qualification to ensure candidates have the necessary academic background for the trade.
4.2 Apprenticeships and Vocational Training
Apprenticeships and vocational training provide hands-on experience with manual machinery, teaching precision machining and tool operation. These programs combine classroom instruction with practical workshops, allowing aspiring machinists to develop technical skills and industry standards. Vocational schools offer specialized courses, while apprenticeships under experienced machinists further refine expertise, preparing individuals for entry-level roles and professional certifications in the field.
4.3 Certifications and Specializations
Certifications and specializations enhance a manual machinist’s expertise and career prospects. Certifications like NIMS (National Institute for Metalworking Skills) or CNC machining accreditation demonstrate proficiency. Specializations, such as precision grinding or tool making, allow machinists to excel in niche areas. Advanced courses in blueprint reading or metallurgy further broaden skill sets, enabling professionals to tackle complex projects and pursue senior roles with confidence and competitiveness in the job market.
Work Environment and Conditions
Manual machinists typically work in machine shops or manufacturing facilities, often in noisy environments requiring prolonged standing. Safety is critical, with use of PPE like gloves and safety glasses.
5.1 Typical Workplace Settings
Manual machinists primarily work in machine shops, manufacturing facilities, or industrial plants. They are often employed in industries such as aerospace, automotive, and precision engineering. Workplaces are typically equipped with manual machine tools, requiring a clean, organized environment. Noise levels can be high, and working collaboratively with other professionals is common. Attention to safety protocols is essential in these settings.
5.2 Physical and Safety Requirements
Manual machinists must withstand long periods of standing and lifting. They handle heavy tools and materials, requiring physical stamina. Safety is critical; they wear protective gear like gloves and safety glasses. Adherence to safety protocols is essential to prevent injuries from machinery and sharp objects. A clean, well-organized workspace also minimizes hazards, ensuring a safer environment for precise and efficient work.
Common Tools and Equipment Used
Manual machinists use lathes, milling machines, grinders, and drill presses to cut, shape, and finish metal and other materials with precision. These tools are essential for their work.
6.1 Manual Lathes and Milling Machines
Manual lathes and milling machines are fundamental tools for machinists, enabling precise cutting and shaping of materials. Lathes spin materials for symmetric shaping, while milling machines remove material via rotating cutters. Both require skill for accurate results, making them indispensable in producing custom parts and components.
6.2 Grinders, Drill Presses, and Other Tools
Grinders are used for polishing and smoothing surfaces, ensuring precise finishes. Drill presses perform accurate drilling operations, while other tools like saws and sanders assist in cutting and refining materials. These tools are essential for achieving specific textures and dimensions, complementing the work done on lathes and milling machines to meet exact project specifications.
6.3 Measuring and Testing Instruments
Manual machinists rely on precision measuring tools like micrometers, calipers, and dial indicators to ensure accurate dimensions. These instruments are critical for verifying part specifications, checking surface finishes, and maintaining tight tolerances. Proper use of measuring tools guarantees the quality and fit of components, making them indispensable in achieving precise and reliable machining outcomes.
Career Path and Advancement Opportunities
Manual machinists can advance from entry-level positions to senior roles by gaining experience and specialized skills over time, leading to increased responsibility and leadership opportunities.
7.1 Entry-Level Positions and Growth
Entry-level manual machinists typically begin by performing basic machining tasks, such as setting up tools and operating lathes or grinders under supervision. As they gain experience, they develop precision skills and learn to interpret blueprints, leading to increased responsibility and opportunities for specialization. This foundational phase is crucial for building the technical expertise needed for career advancement in the field.
7.2 Specializations and Senior Roles
Experienced manual machinists can specialize in specific machinery, such as precision grinding or milling, enhancing their expertise. Senior roles often involve supervising junior machinists, optimizing production processes, and handling complex projects. With advanced skills and years of experience, they may take on leadership positions or become master machinists, ensuring high-quality output and mentoring newer professionals in the trade.
Job Market and Demand
Manual machinists are in demand across industries like aerospace, automotive, and manufacturing, with steady growth due to the need for precision metal components and skilled craftsmanship.
8.1 Industry Trends and Outlook
The demand for manual machinists remains steady, driven by industries requiring precision metal components. Despite advancements in CNC machining, traditional skills are still valued for customization and intricate parts. The aerospace, automotive, and manufacturing sectors particularly rely on manual machinists for high-precision work. As industries evolve, the integration of manual machining with modern technologies ensures sustained relevance and growth in this trade.
8.2 Key Industries Hiring Manual Machinists
Manual machinists are in demand across various industries, including aerospace, automotive, shipbuilding, and defense. These sectors rely on precision metal components, making manual machinists essential. Additionally, industries like machinery manufacturing and precision instrumentation frequently require their expertise. The demand for skilled tradespeople in these fields ensures consistent career opportunities and underscores the importance of manual machining in modern production processes.
Salary Expectations
Manual machinists typically earn competitive salaries, with averages ranging from $40,000 to $70,000 annually, depending on experience, location, and industry. Skilled professionals often see higher pay.
9.1 Average Salary Ranges
Manual machinists generally earn between $40,000 and $70,000 annually, depending on location, experience, and industry. Entry-level positions may start around $35,000, while senior roles can exceed $80,000 with specialized skills and certifications.
9.2 Factors Influencing Compensation
Compensation for manual machinists varies based on factors like location, experience, and certifications. Those in high-demand areas or with specialized skills, such as CNC machining, may earn higher wages. Additionally, industry-specific requirements and the complexity of projects can significantly influence salary levels.
Common Challenges in the Role
Manual machinists face challenges like maintaining precision, adhering to strict safety protocols, and dealing with physical demands such as standing for long periods and handling heavy machinery.
10.1 Precision and Accuracy Requirements
Manual machinists must consistently deliver high precision, ensuring parts meet exact specifications. This requires meticulous attention to detail and adherence to blueprints, often involving precise measurements and adjustments. Even minor deviations can render parts unusable, emphasizing the importance of skill and focus in maintaining accuracy throughout the machining process.
10.2 Physical Demands and Safety Concerns
Manual machinists often work in physically demanding environments, requiring standing for long periods and lifting heavy materials. The job involves handling sharp tools and machinery, posing safety risks if proper precautions aren’t taken. Protective gear like gloves and safety glasses is essential. Additionally, working with loud machinery necessitates hearing protection, and adherence to safety protocols is critical to prevent accidents and ensure a safe working environment.
Safety Protocols and Best Practices
Manual machinists face physical demands like standing for long periods and lifting heavy materials. Safety concerns include handling sharp tools and machinery, requiring protective gear and adherence to protocols to prevent accidents and ensure a secure work environment.
11.1 Personal Protective Equipment (PPE)
Manual machinists must wear safety goggles, gloves, and steel-toe boots to prevent injuries. Face shields and hearing protection are essential when operating machinery. Proper PPE usage, regular inspections, and adherence to safety protocols ensure a secure working environment and compliance with industry safety standards.
11.2 Machine Safety and Maintenance
Manual machinists must perform routine inspections and maintenance on machinery to ensure smooth operation. Regular lubrication, cleaning, and replacing worn parts are critical. Adhering to safety protocols, such as locking out machinery during maintenance, prevents accidents. Proper tool storage and workspace organization also contribute to a safe environment. Neglecting maintenance can lead to equipment failure and workplace injuries, emphasizing the importance of diligence in machine care.
Manual Machining vs. CNC Machining
Manual machining relies on operator skill to guide tools, while CNC machining uses computerized automation for precision and efficiency, reducing human error in complex tasks.
12.1 Key Differences in Operations
Manual machining involves hands-on operation of tools like lathes and mills, requiring operator expertise for precision. CNC machining uses computerized systems to automate tasks, enhancing speed and consistency. Manual machining is ideal for small batches or unique parts, while CNC excels in large-scale, repetitive production. Both methods coexist, each suited for specific manufacturing needs and complexities;
12.2 When to Choose Manual Machining
Manual machining is ideal for small production runs, unique parts, or when complex setups are unnecessary. It excels in creating custom components with precise tolerances, leveraging the skill of experienced machinists. This method is cost-effective for simple tasks and when CNC machining isn’t available or practical. It ensures flexibility and adaptability in manufacturing processes where automation isn’t beneficial.
Everyday Tasks and Operations
Manual machinists perform cutting, shaping, and grinding operations, using tools like lathes and milling machines. They also inspect parts for quality and precision to ensure accuracy.
13.1 Cutting, Grinding, and Finishing
Manual machinists utilize lathes, grinders, and milling machines to cut and shape metal components. They perform precision grinding to achieve smooth finishes and use drills and saws for accurate cuts. Finishing involves polishing and deburring to meet specifications, ensuring final products are free from imperfections and adhere to strict tolerances for optimal performance and durability.
13.2 Assembly and Quality Control
Manual machinists are responsible for the assembly and quality control of components, ensuring they fit and function as intended. Using precise tools and blueprints, they meticulously align parts. Quality control involves inspecting each piece for dimensional accuracy and surface finish, adhering strictly to specifications. This meticulous process ensures the delivery of reliable, high-performance, and durable final products that meet customer expectations and industry standards.
The Role of Manual Machinists in Modern Manufacturing
Manual machinists play a vital role in modern manufacturing by producing precision components that drive innovation and ensure operational excellence across various industries.
14.1 Contribution to Production and Innovation
Manual machinists contribute significantly to production by crafting precise, high-quality components essential for manufacturing. Their expertise enables innovation, allowing industries to develop complex machinery and tools that meet exact specifications and drive technological advancements. This hands-on, detail-oriented work ensures reliability and efficiency in production processes, making manual machinists indispensable in modern manufacturing environments.
14.2 Collaboration with Other Trades
Manual machinists often collaborate with engineers, welders, and other trades to ensure parts align and function seamlessly. Effective teamwork and communication are crucial for interpreting blueprints and achieving production goals. By working together, they solve challenges and optimize workflows, contributing to overall project success and maintaining high standards of quality and efficiency in manufacturing processes.
Continuous Learning and Adaptation
Manual machinists must stay updated with new techniques and technologies to remain competitive. Adaptability is key to mastering evolving tools and processes efficiently in the industry.
15.1 Staying Updated with New Techniques
Manual machinists must continuously update their skills to keep pace with advancements in machinery and manufacturing processes. Engaging in vocational training, workshops, and industry certifications helps them master new techniques and technologies, ensuring they remain proficient in an ever-evolving field. Staying informed about emerging tools and methods is crucial for maintaining precision and efficiency in their work.
15.2 Importance of Problem-Solving Skills
Problem-solving skills are essential for manual machinists, as they often encounter unexpected challenges during production. Diagnosing machine errors, adjusting tool settings, and refining techniques require critical thinking. Strong analytical abilities enable machinists to optimize processes, reduce errors, and improve efficiency. These skills are vital for maintaining precision, ensuring safety, and driving innovation in the workshop, making them indispensable in a dynamic manufacturing environment.
A manual machinist is a vital contributor to modern manufacturing, delivering precision and craftsmanship. Their expertise ensures high-quality production, making them indispensable in various industries.
16.1 Summary of the Manual Machinist Profession
A manual machinist is a skilled professional who operates and maintains traditional machine tools to produce precise metal components. They require strong technical knowledge, attention to detail, and physical stamina. This role is essential in manufacturing, contributing to the creation of high-quality parts and tools. Manual machinists collaborate with other trades to ensure efficient production, making them vital to various industries.
16.2 Final Thoughts on Career Prospects
The manual machinist profession offers stable career prospects, driven by demand for precision metal components in industries like aerospace and automotive. While CNC machining grows, manual skills remain vital for complex, custom projects. Continuous learning and adaptability are key to thriving in this evolving field, with opportunities for specialization and advancement in senior roles or leadership positions.