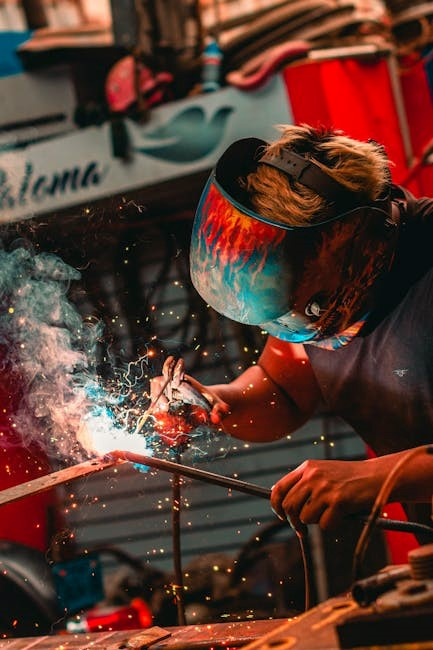
Welcome to our guide on TIG welding filler rods. These essential tools enhance weld quality and strength, with resources like charts aiding in selection and application.
Overview of TIG Welding and Filler Rods
TIG (Tungsten Inert Gas) welding, also known as GTAW (Gas Tungsten Arc Welding), is a precise and versatile welding process. It uses a non-consumable tungsten electrode to produce high-quality welds. Filler rods are optional but often used to add material to the weld pool, enhancing strength and durability. The process is ideal for thin materials and complex joints. Filler rods are classified by organizations like AWS, with designations indicating their composition and strength. Charts, such as the Hobart Filler Metal Chart, guide welders in selecting the right rod for specific materials and applications, ensuring compatibility and optimal weld properties.
Importance of Filler Rods in TIG Welding
Filler rods play a crucial role in TIG welding, enhancing weld quality and ensuring strong, durable joints. They provide additional material to the weld pool, which is essential for achieving desired strength and appearance. Filler rods are particularly important when welding materials like aluminum or stainless steel, where maintaining chemical composition and mechanical properties is critical. They also help bridge gaps and prevent defects like porosity. By selecting the right filler rod, welders can ensure compatibility with the base metal, optimize weld penetration, and achieve the desired aesthetic and structural integrity. This makes filler rods indispensable for professional and precise TIG welding outcomes.
Classification of TIG Welding Filler Rods
TIG welding filler rods are classified based on their composition and properties, with designations like ER70S-6, ER4043, and ER5356. These classifications help ensure compatibility and performance.
AWS Classification System for Filler Rods
The AWS (American Welding Society) classification system categorizes TIG filler rods based on their composition and properties. Designations like ER70S-6, ER4043, and ER5356 provide critical information. The “ER” prefix indicates the filler metal can be used as an electrode or rod. The number following “ER” represents the tensile strength in thousands of pounds per square inch (psi). The letter “S” denotes a solid electrode or rod, while numbers after the hyphen signify specific chemical compositions. This system ensures compatibility with base metals and welding goals, helping welders select the right filler rod for their application, as detailed in resources like the TIG welding filler rod chart PDF.
Common Types of TIG Filler Rods (e.g., ER70S-6, ER4043, ER5356)
ER70S-6 is a popular TIG filler rod for mild steel, offering excellent strength and versatility across various applications. ER4043, a 5% silicon aluminum alloy, is ideal for welding alloys like 6061, providing smooth flow but darkening when anodized. ER5356, containing magnesium, offers high strength and durability, making it perfect for marine applications, though less fluid than ER4043. These rods are widely used due to their compatibility with common base metals, as outlined in resources like the TIG welding filler rod chart PDF, ensuring optimal weld quality and performance for specific materials and projects.
Selection Criteria for TIG Welding Filler Rods
Material compatibility, weld strength, and application-specific needs guide filler rod selection, with charts like the TIG welding filler rod chart PDF aiding in optimal choices for projects.
Material Compatibility and Welding Goals
Material compatibility and welding goals are critical in selecting TIG filler rods. A filler rod chart helps match base metals with suitable rods, ensuring weld integrity. For instance, ER70S-6 is ideal for mild steel, offering 70,000 psi tensile strength, while ER4043 and ER5356 are commonly used for aluminum, with 4043 suited for 6061 alloys and 5356 for 5000 series, providing excellent corrosion resistance. The AWS classification system guides these choices, ensuring rods meet specific tensile strengths and chemical compositions. By aligning the filler rod with the base metal and project requirements, welders achieve strong, durable results that meet their objectives. Proper selection prevents issues like brittleness or porosity, ensuring optimal weld quality and performance.
Size and Thickness Considerations
Selecting the right filler rod size is crucial for achieving high-quality TIG welds. Thicker rods are typically used for heavier materials or multi-pass welds, while thinner rods are ideal for thinner materials or precision work. The size of the filler rod affects heat input, fusion, and the overall appearance of the weld. A filler rod chart can help determine the appropriate size based on the base metal thickness and welding goals. For example, a 1/16-inch rod might be suitable for thin aluminum, while a 3/32-inch rod is better for thicker steel. Proper sizing ensures consistent penetration and avoids issues like lack of fusion or excessive spatter. Always refer to a TIG welding chart for precise recommendations. Size selection is a balance between material thickness and desired weld aesthetics. Using the correct diameter enhances weld quality and efficiency. Choosing the wrong size can lead to poor penetration or uneven welds. A filler rod chart simplifies this process, providing clear guidelines for various applications. This ensures optimal results and minimizes waste. By matching the rod size to the material thickness, welders can achieve professional-grade finishes consistently. Proper sizing is essential for both strength and appearance. A well-chosen filler rod size ensures the weld meets both functional and aesthetic requirements. Always consult a reliable chart to make informed decisions. Material thickness and welding goals are key factors in selecting the ideal filler rod size. This ensures the best possible outcome for any TIG welding project. Proper sizing is a fundamental aspect of successful TIG welding. A filler rod chart is an invaluable tool for making accurate size selections. It helps welders avoid common pitfalls and achieve consistent, high-quality results. By aligning the filler rod size with the material thickness, welders can ensure strong, durable, and visually appealing welds. Always prioritize proper sizing for optimal outcomes. A TIG welding chart is the go-to resource for determining the correct filler rod size. It provides clear guidelines based on material thickness and welding objectives. Using the right size enhances weld quality and efficiency, while the wrong size can lead to subpar results. Proper filler rod sizing is a critical step in the TIG welding process. A chart simplifies this decision, ensuring welders select the ideal size for their specific needs. This leads to stronger, more precise welds. Always refer to a filler rod chart to ensure the correct size is chosen. Size and thickness considerations are vital for achieving the best possible welds in TIG welding. A chart provides the necessary guidance to make informed decisions. Proper sizing enhances both the strength and appearance of the weld, making it a key factor in successful projects. Always use a filler rod chart to select the right size for your TIG welding needs. This ensures optimal results and minimizes the risk of defects. Size and thickness considerations are essential for achieving professional-grade TIG welds. A filler rod chart is the ultimate guide for making the right choice. By selecting the appropriate size, welders can ensure their work meets both functional and aesthetic standards. Proper sizing is a cornerstone of successful TIG welding. Always consult a chart to determine the ideal filler rod size for your project. This ensures the best possible outcome and minimizes potential issues. Size and thickness considerations play a significant role in TIG welding success. A chart provides the clarity needed to select the right filler rod size. Proper sizing ensures strong, durable, and visually appealing welds. Always prioritize accurate size selection for optimal results. A filler rod chart is an indispensable tool for any TIG welding project. It offers clear guidelines for choosing the right size based on material thickness and welding goals. Proper sizing enhances weld quality and efficiency, while incorrect sizing can lead to poor outcomes. Always refer to a chart to ensure the best results. Size and thickness considerations are crucial for achieving high-quality TIG welds. A filler rod chart provides the necessary information to select the ideal size for any project. Proper sizing ensures strong, precise welds that meet both functional and aesthetic requirements. Always use a chart to guide your filler rod size selection. This ensures optimal results and minimizes the risk of defects. Size and thickness considerations are vital for successful TIG welding. A chart simplifies the process of selecting the right filler rod size, ensuring the best possible outcomes. Proper sizing enhances weld quality and efficiency, making it a key factor in achieving professional-grade results. Always consult a filler rod chart for accurate size selection. Size and thickness considerations are essential for achieving strong, durable, and visually appealing TIG welds. A chart provides the necessary guidance to choose the right filler rod size for any project. Proper sizing ensures optimal results and minimizes potential issues. Always refer to a chart to select the ideal size for your TIG welding needs. This ensures the best possible outcome and enhances overall weld quality. Size and thickness considerations are critical in TIG welding for achieving high-quality results. A filler rod chart offers clear guidelines for selecting the right size based on material thickness and welding goals. Proper sizing ensures strong, precise welds that meet both functional and aesthetic standards. Always use a chart to determine the ideal filler rod size for your project. This ensures optimal results and minimizes the risk of defects. Size and thickness considerations are essential for successful TIG welding. A chart provides the necessary information to select the right filler rod size, ensuring the best possible outcomes. Proper sizing enhances weld quality and efficiency, leading to professional-grade results; Always consult a chart to choose the correct size for your specific needs. Size and thickness considerations are vital for achieving high-quality TIG welds. A filler rod chart is the ultimate guide for selecting the right size, ensuring strong, durable, and visually appealing results. Proper sizing minimizes potential issues and enhances overall weld quality. Always refer to a chart to select the ideal filler rod size for your project. This ensures the best possible outcome and meets both functional and aesthetic requirements. Size and thickness considerations are crucial for successful TIG welding. A chart provides clear guidelines for selecting the right filler rod size, ensuring optimal results. Proper sizing enhances weld quality and efficiency, making it a key factor in achieving professional-grade finishes. Always consult a chart to determine the ideal size for your specific needs. Size and thickness considerations are essential for achieving the best possible TIG welds. A filler rod chart offers the necessary guidance to select the right size, ensuring strong, precise welds that meet both functional and aesthetic standards. Proper sizing minimizes potential issues and enhances overall quality. Always use a chart to guide your filler rod size selection. This ensures the best outcomes and minimizes defects. Size and thickness considerations are critical in TIG welding for achieving high-quality results. A chart provides the necessary information to select the right filler rod size, ensuring optimal outcomes. Proper sizing enhances weld quality and efficiency, leading to professional-grade results. Always refer to a chart to choose the correct size for your specific needs. Size and thickness considerations are vital for successful TIG welding. A chart simplifies the process of selecting the right filler rod size, ensuring the best possible results. Proper sizing ensures strong, durable welds that meet both functional and aesthetic requirements. Always consult a chart to determine the ideal size for your project. Size and thickness considerations are essential for achieving high-quality TIG welds. A filler rod chart provides the necessary guidelines to select the right size, ensuring optimal results. Proper sizing enhances weld quality and efficiency, making it a key factor in achieving professional-grade finishes. Always use a chart to guide your filler rod size selection. This ensures the best possible outcomes and minimizes potential issues. Size and thickness considerations are crucial for successful TIG welding. A chart offers clear guidelines for selecting the right filler rod size, ensuring strong, precise welds that meet both functional and aesthetic standards. Proper sizing minimizes defects and enhances overall quality. Always refer to a chart to choose the correct size for your specific needs; Size and thickness considerations are essential for achieving the best possible TIG welds. A filler rod chart provides the necessary information to select the right size, ensuring optimal results. Proper sizing enhances weld quality and efficiency, leading to professional-grade outcomes. Always consult a chart to determine the ideal filler rod size for your project. Size and thickness considerations are critical in TIG welding for achieving high-quality results. A chart simplifies the process of selecting the right filler rod size, ensuring the best possible outcomes. Proper sizing ensures strong, durable welds that meet both functional and aesthetic requirements. Always use a chart to guide your filler rod size selection. This ensures the best results and minimizes potential issues. Size and thickness considerations are vital for successful TIG welding. A chart provides the necessary guidance to select the right filler
Types of TIG Welding Filler Rods
TIG welding filler rods vary by material, including mild steel, aluminum, and stainless steel, each with specific classifications like ER70S-6, ER4043, and ER308, catering to different welding needs.
Mild Steel Filler Rods (AWS A5.18 Specification)
Mild steel filler rods, classified under the AWS A5.18 specification, are a popular choice for TIG welding due to their ease of use and cost-effectiveness. These rods are ideal for welding low-carbon steel materials and are known for their excellent weldability and consistent results. They are widely used in various applications, including general fabrication and repair work, due to their ability to produce strong, durable welds with minimal porosity. The AWS A5.18 specification ensures these filler rods meet rigorous quality standards, making them a reliable option for both novice and experienced welders.
The mild steel filler rods are suitable for welding a range of steel types, from thin sheets to thicker plates, and are often preferred for their smooth, slag-free welds. Their low carbon content reduces the risk of carbide precipitation, ensuring a stable microstructure in the weld area. This makes them particularly effective for applications where corrosion resistance and mechanical strength are critical. As a result, mild steel filler rods remain a cornerstone in TIG welding, offering versatility and performance across diverse industrial and DIY projects.
Aluminum Filler Rods (4043 vs. 5356)
Aluminum filler rods 4043 and 5356 are the most commonly used for TIG welding aluminum. The 4043 rod, a 5% silicon alloy, is ideal for welding 6061, 3003, and aluminum castings. It flows smoothly but may result in darker welds when anodized. The 5356 rod, containing 5% magnesium, offers higher strength and corrosion resistance, making it suitable for marine applications and welding 6061 and 5083 materials. While both are versatile, 4043 is preferred for general use, and 5356 is chosen for applications requiring enhanced mechanical properties. Both are covered under the AWS A5.10 specification, ensuring quality and consistency.
Best Practices for TIG Welding with Filler Rods
Stainless Steel Filler Rods (e.g., ER308, ER309)
Stainless steel filler rods like ER308 and ER309 are designed for welding stainless steel materials. ER308, composed of 308 stainless steel, is ideal for welding 304 stainless steel, providing excellent strength and corrosion resistance. ER309, made from 309 stainless steel, is better suited for high-temperature applications and offers superior resistance to corrosion and cracking. Both rods are classified under the AWS A5.9 specification, ensuring consistent quality. They are widely used in industries requiring durable and long-lasting welds, such as food processing, medical equipment, and marine hardware. Proper selection ensures optimal weld quality and performance in demanding environments.